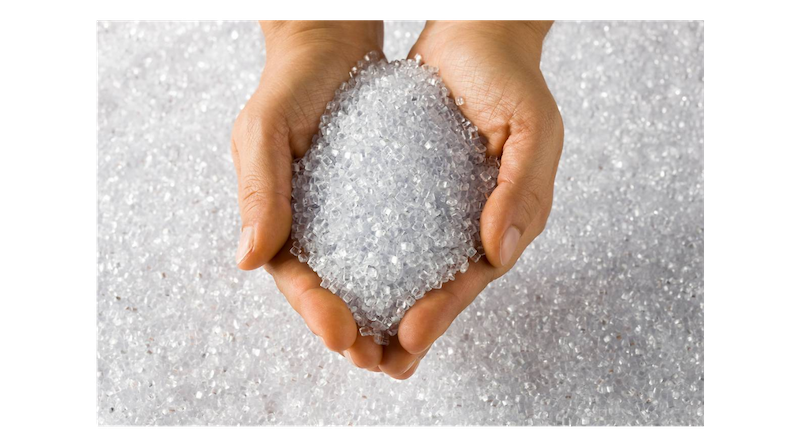
Chemical recycling: a contribution to the EU strategic industrial autonomy
Citeo, the French company in charge of Extended Producer Responsibility (EPR) for household packaging and graphic papers, fully supports the efforts to develop new complementary recycling technologies, among which chemical recycling, as a solution to accelerate the circular economy and the EU strategic industrial autonomy
Global plastics production has surged over the past 50 years, from 15 million tonnes in 1964 to 350 million tonnes in 2019 and is expected to double again over the next 20 years. Rapid production growth combined with low collection rates and on-going technical and economic barriers to plastics recycling have made plastics a global issue.
Pollution caused by the accumulation of plastic waste and its leakage into the environment is the most concerning environmental problem in many countries and has drawn the attention of public and private actors worldwide.
In recent years, many governments and international institutions have set ambitious waste reduction and recycling targets.
The European Commission has now accelerated the movement to close the loop through the new Circular Economy Action Plan, under the EU Green Deal, with a main focus on plastics and packaging; and the EU recovery plan with a specific national contribution on non-recycled plastics packaging. The proposed measures, both at the national and European levels, include several that are directly related to the recycling of plastic packaging: limiting single-use plastics with the aim of 100% of plastic packaging being reusable and recyclable by 2030, promoting eco-design and stimulating technological innovation, and developing international standards for the sorting and recycling of plastics.
As part of this growing trend, France recently implemented additional measures to increase recycling of materials and limit single-use plastics under its act of law against waste and for a circular economy.
This general movement is driving the transition from the linear “produce, consume, throw away” model to a circular model in which plastic waste is diverted from landfills and oceans and fed back into the economy through already existing or nascent recycling technologies, such as producing recovered feedstock. To ensure the full potential of this transition is realised is, however, dependent on technological breakthroughs and greater cooperation between actors in the plastics value chain.
The need to promote new solutions to recycle plastics
Plastics waste is hurting the environment when it is not sorted efficiently. In this perspective, all over the world, governments and international organisations are making known their desire to increase the plastic recycling rate in an effort to end the pollution caused by plastic waste, especially in our seas. And businesses are right there with them: today, many companies publicise their desire to use recyclable and recycled plastics in their packaging. These voluntary statements provide a direction, but we still need to find the right path, because plastic is not like other materials
Chemical players, the suppliers of plastic raw materials, as well as waste managers, recyclers, brand owners, and others are adding a new dimension to the industry to help solve the waste problem and tackle the issue at its very core.
Being a product of the oil industry, plastic is composed of molecules of organic polymers that are not as easy to recycle as metals, for example. Made up of several resins, it is also commonly combined with additives and fillers that make packaging more useful, but which also complicate the recycling process. And ultimately, once used, plastic packaging can be left dirty by the products it served to protect. For all type of resin expect clear PET, mechanical recycling cannot reach food contact grade for recyclates.
These different constraints make plastic recycling an industrial challenge. The technological leap may come from research and development in polymers (depolymerisation, dissolution, distillation, purification, repolymerisation, etc.), or even biology (enzymatic depolymerisation). These processes are collectively referred to as “Chemical Recycling” Indeed, these are the fields in which we have seen numerous new projects over the past decade, several of which are now entering the industrial phase.
Citeo’s key role to promote new solutions to recycle plastics
These new technologies are the central theme of the Plastic Solutions Forum that Citeo has organised on the 5th & 6th October 2020. Complementing current recycling processes, they can accelerate plastic’s transition into a circular economy, thereby helping to conserve our resources and protect our environment.
Furthermore, as part of Citeo’s call for projects to promote eco-design and recycling and recovery projects for plastic and paper in France, leading international energy company Total, plastic recycling technology provider, and global brands such as Nestlé and Mars today joined forces to develop an innovative industrial chemical recycling industry in France.
The first-of-a-kind consortium of world-leading players from across the plastic packaging value chain will examine the technical and economic feasibility of recycling complex plastic waste, such as small, flexible and multi-layered food-grade packaging or for made of polystyrene packaging.
These products are currently considered non-recyclable and are therefore either incinerated or disposed of in landfills.
Those ambitious projects meet Citeo’s overarching goal of finding end-to-end solutions for all packaging. New recycling technologies, such as chemical recycling, will take plastic performance to the next level and accelerate the circular economy for post-consumer plastic waste, especially when it is complex. Especially by addressing the circular economy challenges of food-grade plastics, chemical recycling is complementary to the existing mechanical recycling activities.
The need for political action
Recycled plastics are currently seen as worthless by most manufacturers who prefer higher-grade virgin materials. Since those also happen to be cheaper and less likely to be contaminated by legacy substances, Europe’s recycled plastics can often end up in poor value products at best or in landfills or in incineration plants when they are not shipped abroad.
This is where “chemical recycling” comes in. The technique holds the promise to tackling some of the most difficult challenges of current recycling efforts in Europe. Plastic is and remains a key element of our everyday life and has a number of benefits for society as well as the environment if waste management issues are addressed successfully. In this perspective, a life-cycle approach needs to be followed in order to consider all the possible benefits and risks of this new approach, including on climate.
Concretely, chemical recycling should be able to isolate toxic substances contained in plastics, which are now banned in Europe, making it possible to retrieve feedstocks that can be used to manufacture products which are as good as new. Questions remain and must be answered like the efficiency of the process, the economy, the way to address the recycling rate through the mass balance approach, environmental impact but the opportunity in such chemical technologies, in contrast to mechanical ones, is that they generate virgin-grade feedstock which can then be used to make new materials and chemicals of virgin-grade quality, ensuring a circular loop of plastics and competitivity between virgin and secondary raw materials.
In this regard,
the European Commission should work on aligning existing regulations and legislations on chemicals, waste and products in order to guarantee that products and packaging are exempted from substances of concerns, in line with the Commission’s Chemicals Strategy for Sustainability that has just been published.
Finally, such solutions, to complement mechanical recycling and reach EU targets on plastics and on its autonomy, could represent a profit pool of nearly 50 billion euros per year worldwide by 2030 according to McKinsey. The true potential for chemical recycling to become profitable depends on the sufficient supply of suitable plastic feedstock, and the further development of pyrolysis and gasification technologies to produce high volumes of recycled plastics with consistent quality at a competitive price. But reaching that potential also depends on conducive regulatory framework. This is why the European Commission needs to address further incentives and regulatory measures to increase the recyclability of plastics and make it a valuable resource, in line with the targets of the Critical Raw Materials Strategy and the upcoming Chemicals Strategy for Sustainability.