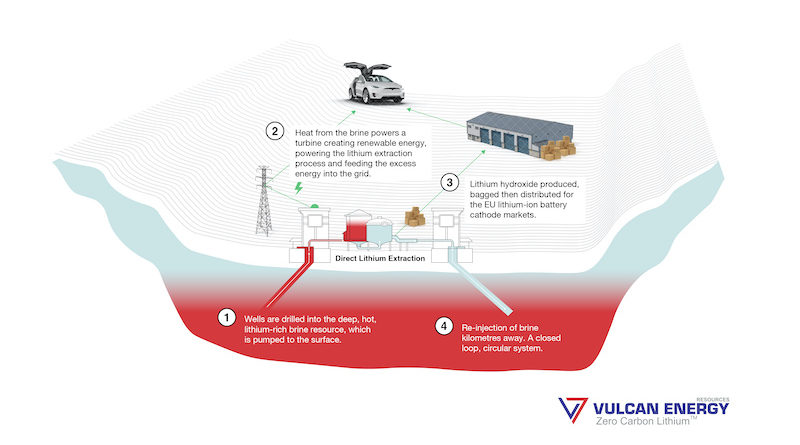
Vulcan Energy: Decarbonising and de-risking the European Electric Vehicles Supply Chain Starts with Lithium
As the world positions for a more sustainable future, mining of lithium will continue to rapidly grow, and so too will OEMs and policy makers demand for greener processing practices.
Europe is set to become the second largest consumer of lithium in the world after Asia following a dramatic growth in electric vehicles (EV) production. Today, there is actually more investment going into electric mobility in Europe than in China. Those EV require lithium-ion batteries and Europe has also become the fastest growing lithium-ion battery production centre in the world.
But Europe is facing a major problem. Despite the EU’s stated goal to develop a fully integrated supply chain locally, there is currently zero lithium extraction and production here and Europe will have to rely entirely an imported material, 80% of it coming from China. But sourcing from China poses two major and obvious issues: supply chain risk and environmental impact.
On the supply side, de-risking supply-chains is crucial following rising tensions in international trade but also following events such as Covid19 which showed that Europe is massively dependent on China for vital supplies ranging from pharmaceuticals to lithium.
On the environmental side, CO2 emissions linked to lithium production in China are the highest in the world and does not match with automakers’ goal to become carbon neutral.
Simply maintaining current production techniques could be defeating the purpose of clean Electric Vehicles. Calculations suggest that if we convert every single traditional car into an EV, and that the lithium-ion batteries fitted in those EVs use material produced by existing production methods [Extracting hard rock in Australia, shipping on large vessels to China and then processing in coal-fired operations] then lithium production alone will generate more than 1 billion tons of CO2 emissions.
That’s more than the annual CO2 emissions of the UK, France and Italy combined.
Driving an EV is not enough to decarbonize the world, we need to look at the entire supply chain, starting with mining, and shake the industry up from the core.
Vulcan Energy Resources is a company aiming to decarbonize the currently high carbon footprint of lithium-ion batteries used in electric vehicles, by producing a unique, world-first Zero Carbon LithiumTM product from its Vulcan Project in Germany. The company will be producing both battery grade lithium and renewable energy from geothermal brines located in Germany. The project is actually located in the centre of the automotive and lithium-ion battery industry, just 60km from Stuttgart.
The only alternative for European lithium consumers today, even they don’t want to purchase lithium from China, is to source it from South America. However, brine operations using evaporation ponds in Chile and Argentina are also linked to a number of environmental concerns including CO2 emissions but mostly water waste, in a place which the driest on earth, where water is precious. Environmental associations and indigenous communities have been fighting against lithium mining in this region for years.
It is difficult to see how lithium mining in this part of the world will keep growing and feed international demand for sustainable lithium without facing major hurdles.
Vulcan’s production method is radically different. Geothermal production is already well developed in Germany and globally but the difference in Germany and more specifically in the Upper Rhine Valley, is that the hot brine that is extracted from the ground contains a high concentration of lithium. It is something that can only be found in two places in the world: in the Salton Sea in California, and in this region of Germany.
The hot brine extracted from the ground generates steam that powers turbines and produces renewable electricity, most of it is sold to the grid and the rest is used for Vulcan’s own process. Instead of just reinjecting the brine into the ground after the renewable energy has been generated, the brine flow is diverted and lithium is extracted from the solution using a Direct Lithium Extraction process. Once the lithium has been extracted, the brine is reinjected in the ground with no waste. The process only takes a few hours instead of months, and is not dependent on weather like in South America.
But most importantly the process has a negative cardon footprint because it generates more green electricity than it consumes.
This is a unique process that will satisfy OEMs’ stated goal to source zero carbon and sustainable raw materials for Electric Vehicles.
And the project has scale. Vulcan has the largest lithium resource in Europe and one of the largest in the world with so far more than 15 million tons of lithium identified, enough to power more than 300 million EV, and large enough to become Europe’s primary source of battery quality lithium hydroxide.
The project is already supported by the EU with a recent investment secured from InnoEnergy, the group steering the European Battery Alliance.
Vulcan advancing very rapidly, they have published a scoping study in February and will be releasing a Pre-Feasibility study by the end of the year. The company is currently working on a pilot plant design that they will be operating next year and are aiming to start lithium production in 2023 and grow with the European EV market.